目次
製品の角を滑らかに整える面取り加工は、安全性の向上や品質維持に欠かせない重要な工程です。適切な面取りを施すことで、作業者の怪我を防ぎ、部品の耐久性や組み立ての精度を高めることができます。
本記事では、面取りの基本から「糸面取り・C面取り・R面取り」の違い、それぞれの特徴について詳しく解説します。自社の製造工程に合う技術を選ぶ際の参考にしてください。
面取りとは?
面取りとは、素材の角を削り取り滑らかに仕上げる加工技術のことです。金属や木材、ガラスなどのさまざまな素材において、鋭利なエッジを和らげることで安全性を確保し、製品の品質を向上させる重要な役割を果たしています。製造現場で広く用いられ、部品の組み立てをスムーズにする効果も期待できます。
面取りの加工方法には、専用の工作機械を使うものから手作業で行うものまでさまざまな手法があり、求められる精度や仕上がりによって適切な方法が選択されます。精密な部品では機械による加工が必要ですが、仕上げの工程では職人の手作業が加わることもあります。
日本では、機械加工部品のエッジ品質に関する規格が、2004年にJIS規格として制定されました。ただし、これは機械加工された部品を対象としたものであり、板金加工には適用されません。板金加工では、一般的に厳密な規格ではなく、概略的な指示に基づいて面取りすることが多くなっています。
参照元:日本工業規格 JIS
面取りの種類
面取りにはさまざまな方法がありますが、主に「糸面取り」「C面取り」「R面取り」の3つに分類されます。それぞれの加工方法に特徴があり、目的や用途に応じて適切な選択が求められます。
仕上がりの品質やコスト面を考慮しながら、どの面取りを施すか決めましょう。
糸面取り
糸面取りは最も簡易的な面取り方法で、加工後に残るバリやカエリを取り除くために行われます。バリは加工時に生じる微細な突起や鋭利な部分のことで、そのままでは作業者の安全性に影響を及ぼすだけでなく、後工程での精度にも影響を与える可能性があります。
糸面取りは、極めて細かい削り取りをするため、見た目にはほとんど変化が感じられませんが、安全対策として重要な役割を果たすのです。また、大がかりな面取りを行うのが難しい場合の妥協策として用いられるケースもあります。
一般的には低コストで実施できるため、幅広い分野で採用されています。
では、圧倒的に生産量が多い、板金製品のエッジの仕上げ方法とは、どんなものなのでしょうか?
板金図面には、文字で下記のように記載されています。
C面取り
C面取りは、角部に一定の角度で平面を作る面取り方法で、最も一般的に使用される加工の一つです。機械加工の分野では、C0.5やC1.0といったように数値で指定され、精密な加工が求められる場面で多く用いられます。
C面取りの最大の特徴は、エッジを明確に処理しながら、作業性や組み立てのしやすさを向上させる点。また、鋭利な角を取り除くことで安全性を確保し、製品の仕上がりをより均一にすることが可能です。
加工方法としては、切削工具や専用の面取り機を使用し、安定した品質を実現します。機械加工の現場では、C面取りの指示が標準的に盛り込まれており、ほぼすべての加工品で必要とされる技術の一つです。
R面取り
R面取りは、角を滑らかな曲線状に仕上げる加工方法で、見た目の美しさや手触りの向上を目的とする製品に多く用いられます。C面取りとは異なり、直線的なカットではなく、半径を持たせた曲線で処理するため、より滑らかで自然な仕上がりが得られます。
例えば、家電製品や自動車部品、精密機器の外装など、触れる機会の多い製品にはR面取りが施されるのが一般的です。美観を向上させるだけでなく、使用時の安全性を高める役割も果たします。
しかし、C面取りや糸面取りと比べると加工の難易度が高く、高精度な機械や熟練の技術が必要に。そのため、R面取りは加工コストが上昇しやすい傾向がありますが、品質を求める製品では欠かせない工程です。
オーセンテックでは、高度な技術を要するR面取りに対応できる、高性能なバリ取り機を多数提供しています。精度の高いR面取りを実現するには、安定した加工精度をもつ機器が不可欠です。同社の機器は、微細なR形状の加工にも対応し、均一で高品質な仕上がりを可能にします。
製品の品質向上や安全性の確保を求める企業にとって、オーセンテックの技術は大きなメリットをもたらすでしょう。
関連記事>>板金エッジのR面性状
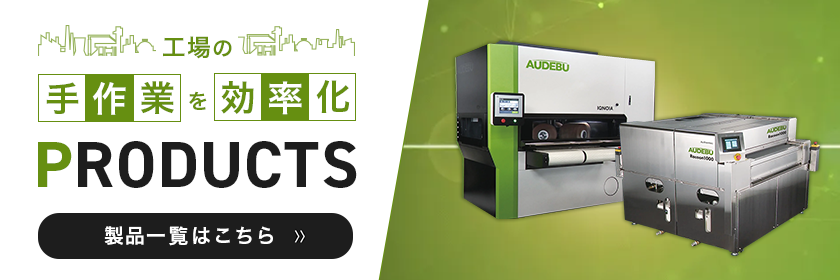
面取りの目的
面取りは、安全性や品質の向上、作業効率の改善を目的として行われる重要な加工です。
ここでは、面取りの主な役割について見ていきましょう。
作業者・使用者の怪我を防ぐ
面取りは、鋭利なエッジやバリを取り除き、作業者や使用者が怪我をしないようにするために行われます。バリが残っていると手を切る危険があり、製品の手触りも悪くなります。
特に手に触れることが多い部品では、安全性を高めるために面取りが欠かせません。
関連記事>>製造物責任法(PL法)とバリ取り
品質を向上させ、故障を防ぐ
部品にバリが残ると、機械の動作中に剥がれて異物混入の原因となり、故障を引き起こす可能性があります。また、摩擦が増えて部品の耐久性が低下することもあります。
面取りを行うことでこれらのリスクを軽減し、安定した動作が実現できるのです。
組み立て性の向上
バリがあると部品の位置がずれやすく、組み立てがスムーズに進まないことがあります。面取りによって角を整えることで、部品同士の嵌合がスムーズになり、組み立て作業の精度が向上します。
作業効率が上がり、製品の仕上がりも安定するでしょう。
関連記事>> 塗装とエッジの関係
面取りの加工方法
それでは続いて、面取りの加工方法について解説します。面取りは作業者の安全を確保するためにも、製品としての品質を確保するためにも重要な作業です。次のような方法で面取りをして、製品の品質を確保してください。
フライス加工
フライス加工は、フライス盤で行う面取りです。テーブルにワークを固定して、バリに対して面取りのための工具を移動させて加工を行います。使用する工具はC面取りであればカッター、R面取りであればRカッターを使用するのが一般的です。面取りをするワークを固定しなければならないため、平面のものにたいして使われる手法となります。平面のワークに対して面取り・糸面取りをするための方法のひとつが、ご紹介したような「フライス加工」と呼ばれる方法です。
旋盤加工
旋盤加工とは、旋盤で行われる面取り加工のことです。一般的にワークの端や穴の周辺、溝にあるバリ取りを行うために採用されます。ワーク自体を回転させて、回転しているワークにバイトを当てて面取り加工を行います。対象となるワークの形状が円柱状でる場合に適した方法です。もしC面取りで使用するのであれば、斜め45°の片刃バイトが用いられ、R面取りの場合は総型バイトもしくは倣い加工にて洗顔加工を行うことが可能です。
ドリル加工
穴のバリを取るためにしか活用されない方法です。しかし穴のバリを取る用途に限っては、瞬時に面取りが終わることがメリットと言えるでしょう。
ヤスリやサンダー等の手作業加工
もし人が面取りをする場合は、ヤスリ・サンダーなどの加工器具を用いて作業を行います。その他、スクレーパー・ロータリーバー・研磨シート・研磨ディスク・研磨ベルトなどが使用されることも少なくありません。ただしヤスリやサンダーなどの手作業用加工器具で行われる面取りは、精度が低くなりがちであることがデメリットです。そのため、糸面取りをする際に適しています。以上のように手作業ではヤスリなどを使いますが、デメリットもあることを知っておいてください。
ブラシ研磨
その中でも、オーセンテックが得意とするブラシ研磨加工は、精度の高い面取りを実現しつつ、効率的な加工が可能な方法として注目されています。
ブラシ研磨加工は、回転するブラシを使用して素材のエッジ部分を削る技術です。特にバリや微細な角の処理に優れており、滑らかな仕上がりを実現できるのが特徴。一般的な切削加工では、細かいエッジの仕上げに手間がかかることがありますが、ブラシ研磨を用いることで、均一な面取りを短時間で可能です。さらに、C面取りやR面取りなど、多様な形状にも対応できるため、幅広い製品に適用可能です。
また、ブラシの硬さや回転速度を調整することで、素材に合わせた最適な仕上げが可能に。例えば、アルミやステンレスなどの金属製品では、強度を保ちつつ不要なバリを除去する設定が求められます。一方で、繊細な加工が必要な部品では、ブラシの圧力を抑え微細なエッジを丁寧に仕上げられるでしょう。
※AuDeBuシリーズのブラシ
【関連記事】バリ取り機のブラシについて
C面取り・R面取り・糸面取りは特徴を押さえて
いかがでしたでしょうか?この記事を読んでいただくことで、C面取り・R面取り・糸面取りについてご理解いただけたと思います。
それぞれ特徴が異なりますので、必要な面取りを行わなければなりません。作業やバリ取り機選びの際に、今回の記事を参考にしてください。
バリ取り機の導入ならオーセンテックまでぜひ一度ご相談ください。
オーセンテックのバリ取り機
オーセンテックのバリ取り機は、優れた仕上がりと作業効率の向上を実現する高性能な機器です。
金属加工において不可欠なバリ取り工程を、自動化技術と独自のブラシシステムにより、精度を損なうことなくスムーズに行います。
従来の手作業によるバリ取りでは均一性にばらつきが出たり、作業者の負担が大きくなったりする課題がありましたが、オーセンテックのバリ取り機を導入することで、これらの問題が大幅に改善されるでしょう。
オーセンテックの製品は、使いやすさにもこだわって設計されており、直感的な操作パネルや視認性の高い構造を採用しています。初めて使用する方でもスムーズに扱えるため、導入後の習熟期間を短縮し、生産ラインへの影響を最小限に抑えることが可能です。
また、洗浄機やワークロボットとの連携機能を備えており、工場の自動化を促進しながら、作業員の負担を軽減することにも貢献します。
さらに、オーセンテックではさまざまなワークサイズに対応した豊富なラインナップを用意しており、用途に応じた最適なバリ取り機が選択可能。
精密な仕上がりが求められる製品から、大型ワークのバリ取りまで、多様なニーズに対応可能です。
高品質な仕上がりと生産性向上を両立したオーセンテックのバリ取り機について、詳しくは製品一覧ページをご覧ください。
オーセンテックのバリ取り機が選ばれる理由
バリ取り機を導入することで、工数が削減され、人手不足や生産性の伸び悩みをいった問題の解決につなげることができます。
私たち、オーセンテックが提供できる強みは大きく2つあります。
オーセンテックのバリ取り機が選ばれる理由
バリ取り機を導入することで、工数が削減され、人手不足や生産性の伸び悩みをいった問題の解決につなげることができます。
私たち、オーセンテックが提供できる強みは大きく2つあります。
圧倒的な仕上がり品質とスピード
弊社が独自に開発したブラシ回転機構と研磨ブラシにより、優れた研磨力とエッジとワーク表面の仕上がり品質の高さを兼ね備えたバリ取り機が誕生しました。
それにより、バリ取りのスピードは、人の手で行うよりも5~10倍速くなり、さらにムラのない安定した品質が実現可能になりました。
初心者にも安心の使いやすさ
バリ取りのスピードや仕上がりだけではなく、操作パネルの使いやすさやメンテナンスのしやすさにもこだわっています。 操作パネルは直感的に操作できるタッチ式を採用、操作や設定変更などの作業が容易に行えるようになっています。
また、メンテナンスのしやすさにもこだわっており、お客様自身で部品交換などの簡易なメンテナンスを行えるよう機械設計をしています。文書や動画のメンテナンスマニュアルは初心者の方でもわかりやすい内容となっています。
実際に使用する方の視点にたった使いやすさを実現しています。
バリ取り機一覧
-
AUDEBU IQNOIA
- 対応ワークサイズ
- 幅:〜1,219mm
- 厚さ:0.1~20mm
-
AUDEBU CX
- 対応ワークサイズ
- 幅:~1,500mm
- 厚さ:0.1~20mm
-
AUDEBU 1000MPF
- 対応ワークサイズ
- 幅:~1,000mm
- 厚さ:0.1~20mm
-
AUDEBU 1300
- 対応ワークサイズ
- 幅:~1,300mm
- 厚さ:0.1~20mm
-
AUDEBU 1000
- 対応ワークサイズ
- 幅:~1,000mm
- 厚さ:0.1~20mm
-
AUDEBU 600
- 対応ワークサイズ
- 幅:~600mm
- 厚さ:0.1~20mm
-
AUDEBU 1000MP
- 対応ワークサイズ
- 幅:~1,000mm
- 厚さ:0.1~20mm
バリ取り機の導入事例
オーセンテックのバリ取り機を導入して、作業効率の向上、人手不足の解消などに繋がった事例をご紹介します。
バリ取り機の導入をご検討の方は、ぜひご相談ください
オーセンテックでは、ヒアリングやサンプル加工などを通じ、お客様の課題と解決方法を明確化し、お客様のお悩みやご予算に応じて、最適なバリ取り機をご提案させていただきます。
バリ取り機の導入をご検討の方、ご不明な点などをお持ちの方は、オーセンテックまで一度ご相談ください。
-
お電話でのお問い合わせ
-
メールでのお問い合わせ
この記事の著者

オーセンテック株式会社
オーセンテック株式会社では、「お客様の声を「アイデア」に お客様の笑顔を「力」に「ものづくり」に貢献する会社でありたい」という企業理念のもと、製造現場の生産性向上・人手不足・品質の安定化・環境改善を実現させるため、手作業をなくすための機械(バリ取り機や板金洗浄機など)を開発・販売・メンテナンスしております。
オーセンテック編集部では、これまでの数多くのバリ取り機、洗浄機の導入事例・サポート経験を活かして、バリ取りや洗浄といった板金加工現場でなくてはならない工程・作業に関するお役立ち情報を発信しています。