【導入機器】
AUDEBU 1000/BlackLine/Racoon
【事業内容】
スチール家具や貨幣処理機、
自動車用精密部品などの板金加工
【選んだ理由】
サンプル試験を実施した結果、
お客様から品質にお墨付きを頂いた
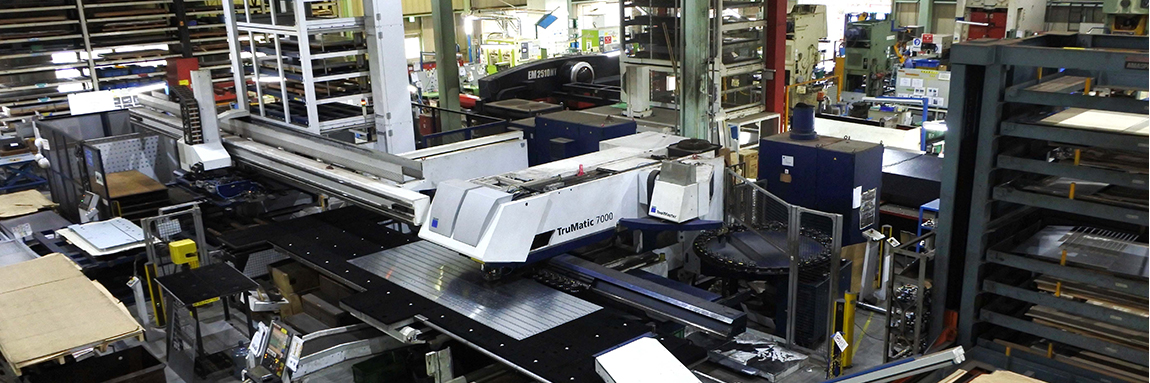
株式會社丸十様の概要
1931年(昭和6年)草刈り鎌の製造会社として創業した株式會社丸十。1960年代に板金加工業に着手してから、スチール家具や貨幣処理機、自動車用精密部品など時代を象徴するような板金加工業に取り組んできました。
板金加工の設備導入はもとより、生産管理システムの導入やISOの取得などにもいち早く取り組んできました。
2005年に従来の本社工場と第二工場を統合して、新たに「Digital IT Factory」というコンセプトを掲げ、Information(情報の伝達)とIntelligence(知力)を生かした高いレベルのモノづくりに取り組んでいます。
株式會社丸十
兵庫県加古川市八幡町上西条306-235
https://kk-marujyu.co.jp/
インタビュアー本日は、株式會社丸十 代表取締役社長 松尾様にお話を伺います。まずは御社の事業内容を含めた会社の紹介をお願いします。
松尾様:丸十は、昭和6年に草刈り鎌を含めた農機具の製造から創業した会社です。戦後の時代の流れにあわせた事業の変換期に、製缶事業を始めてからは、板金加工の需要とともに事業を展開していきました。
当初はロッカーやスチール家具の製作を行っており、昭和50年頃には自動販売機、両替機、トラクターやコンバインなどの農耕器具の機構部品などの製作へと変わっていき、平成時代の高度成長期には精密機器メーカーや建設機器メーカーからの受注と共に弊社も大きく成長していったのです。
その成長の際には、会社設備の自動化も進み、今では医療機器や医薬品の設備機器や物流設備、更には新幹線などの鉄道関係のシート部品の製作にも携わっています。
インタビュアー地域性が強い御社の事業が、農耕器具の製作から板金加工へと変わっていったのも、この地域としてのアドバンテージがあったのでしょうか?
松尾様:兵庫県には、医療機器メーカーや計測機器のメーカーも数多くありましたので、依頼に合わせて、弊社の事業も農耕器具から板金加工へ、そして精密板金加工へと転換していったのです。
インタビュアー多岐にわたる業種のお客様が、御社に相談したり依頼する上での意図や理由には、何があるのでしょうか?
松尾様:弊社の強みとしては、まず10,000㎡という工場の広さでしょうか。工場の建物だけでも6,000㎡あるので、大量な物でも、大きな物でも加工することができます。
後は、板金加工だけでなく、弊社の協力会社との連携で、高度なスペックの塗装やメッキ加工も含めた一貫生産が可能であるということです。表面処理、組立、動作確認、最終検査といった今まで依頼主であるお客様の内製で行われていた部分も含めて最終の完成品まで弊社で行えるところは非常に評価されており、弊社の売り上げの半分を占めるほど受注を頂いています。
インタビュアー量産品を請け負える規模を持っている事と検品まで含めた一貫生産ができるのは、発注者側にとって非常に魅力がありますね。ところで、御社にはベトナムにも工場がありますがベトナムに工場展開をされた理由をお聞かせください。
松尾様:ベトナムに子会社を持ちたいと思ったのは5年程前です。当時から将来的に日本の人口が少なくなると、我々の仕事も人手不足に陥るのでは?という危惧がありました。ベトナム人は勤勉で宗教も仏教徒が多く、比較的日本人と通じる部分が多いという事もあり、国内だけで生産を行うのではなく海外のベトナムにも生産拠点をいち早く置いたわけです。
インタビュアーベトナム工場での生産の割合は、どの位になるのですか?
松尾様:現在、ベトナム工場での仕事の6割は、本社工場からの移管生産です。残りの4割は、現地の日系企業から板金加工の依頼を受けています。
インタビュアーベトナム工場で加工された製品の品質については如何ですか?
松尾様:日本のお客様の多くは、クオリティは日本の規格でコストは下げて欲しいと言われます。
弊社がベトナム工場を作ったコンセプトは、ジャパンクオリティ・ベトナムコストということで提供しています。心配していた品質については大きなダメージや不具合もありませんし、お客様にも喜んでいただいております。
インタビュアーベトナム工場も、順調に稼働されているという事ですね。御社が請け負う加工品の、平均ロットはどれ位なのですか?
松尾様:各メーカーさんによって、バラツキはありますが、平均すると30~50のロットが多いと思います。
弊社の加工品の約8割は、毎月定期的に受注する物から2~3ヶ月毎に発注があるリピート品です。残りの約3割が試作品や1回の発注の物です。
インタビュアー安定した供給が可能な事は、 お客様にとってもメリットがありますし、更に品質が一定であることも安心できますね。その品質の過程で、オーセンテックの機械も一役をかっていると思うのですが、御社がオーセンテックを知ったきっかけを教えてください。
松尾様:弊社の取り扱うワークには、精密な部品が多く含まれています。例えば両替機のように、人が直接手を触れる、お金が通る、お札が通る装置は、機構部品や製品そのものの外観についてもデリケートな扱いを求められることが多いのです。
加工品のバリに関しても、従来は人手でバリ取りの作業をしていましたが、受注増に伴って機械化にすることが出来ないかと思っていたのです。更に、人が作業すると作業者によって、仕上がりにバラツキが生じてしまうという問題もあったので、安定した品質を維持するためには、機械化、そして自動化を可能にする物を探さなくてはいけなかったのです。
だから、10年程前の展示会で、“ブラシを使ってコンベアの上でワークを吸着させてバリを取る”というオーセンテックさんの機械を見つけたときは衝撃で、すぐに導入したのです。
インタビュアー他社でも、同じようにバリを取るメーカーや機械もあるかと思うのですが、比較検討もされたのですか?
松尾様:もちろん、他のメーカーの機械も検討はしましたが、弊社の加工品は材質も様々ですし板厚にも色々な物があります。あらゆるサンプルを試験して検討した上で、お客様からこの品質なら問題が無いとお墨付きを頂いたのがオーセンテックさんのバリ取り機「AuDeBu1000」だったのです。
インタビュアー丸十様では、オーセンテックのAuDeBu1000を2008年に導入された後、2016年にもう一台導入されていますが、その経緯と導入後に気付いた点などを教えてください。
松尾様:何といっても、操作性の良さが際立ちます。
弊社では、数年前からベトナムの実習生12名を本社工場に迎えています。その実習生たちが、自ら段取りをして機械を操作しているのです。
AuDeBu1000のタッチパネル式の操作盤は入力した数値を記憶しているので、手順さえ教えれば誰でも一定品質のバリ取りが可能になるのです。だから、みんながAuDeBu1000を使っている状態です。
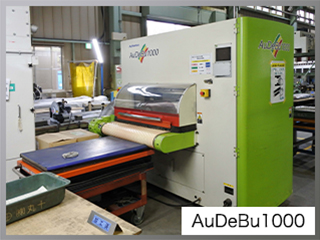
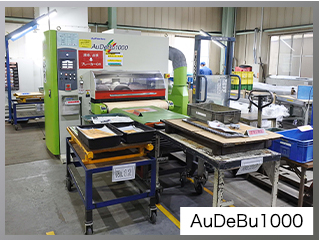
インタビュアー10年前に導入されたAuDeBu1000もまだ稼働しているのですか?
松尾様:最初に導入したAuDeBu1000は、現在ベトナム工場で稼働しています。AuDeBu1000はブラシやコンベアのベルトなどの消耗品を交換してモーターや集塵機のメンテナンスを怠らなければ、何のトラブルも無く今でもバリをしっかりと取ってくれます。
しかし、設備があるだけでただ機械に頼っただけではどこでもできる加工になってしまうので、従業員には機械の特性を熟知した上で加工を進めていけるようスキルアップを期待しています。
それができれば品質も納期も全うする事ができると思いますので、社内のスキルレベルを上げ、そして自動化できるところは自動化を進めていくということが弊社の今後に必要かと思います。
インタビュアー丸十様ではバリ取り機の他にオーセンテックのBlackLineやRacoonも導入されていますが、その経緯やきっかけを教えていただけますか?
松尾様:近年の受注の内容が、薄板の加工から中板、厚板へと移行しています。例えば、物流関係のコンベアや鉄道部品などです。そこではもっと早くバリ取りができないかという要望が多く出てくるのです。厚みのある素材の、酸化被膜や溶着ドロスを、短時間で、しかも同一の加工品質を提供できる機械がオーセンテックさんのBlackLineだったのです。
また、依頼される品物によっては、塗装やメッキをしないで素地のまま納品をして欲しいという受注案件もあります。そういった品物は、タップ部分の油や切子などの汚れを取らないといけないのです。従来は、アルコールやシンナーなどを使って、人の手で作業をしていたのですが、薬品を扱うのは作業者も嫌がりますし何より健康面の心配もあります。無害で自動化できるものを探していたところにオーセンテックさんからRacoonを提案して貰ったのです。
インタビュアーAuDeBu1000で実績のあったオーセンテックの製品だったわけですが実際にBlackLineやRacoonを使用してどのような効果がありましたか?
松尾様:BlackLineは、稼働させてみるとバリ取りの速度がAuDeBu1000と比べて5~ 6倍のスピードでできます。操作用のタッチパネルもコンパクトで非常に使いやすいです。
Racoonについては、洗浄を水でできるというのは驚きでした。水を使用するので、もちろん無害なため、人や環境に優しいです。なによりランニングコストも安価で済みます。しかも大型のワークも入るし、乾燥も早いのでトータルコストでのメリットは大きかったです。手作業でふき取り洗浄をしている時よりバラツキも無くなり、仕上がり品質にもとても満足しています。
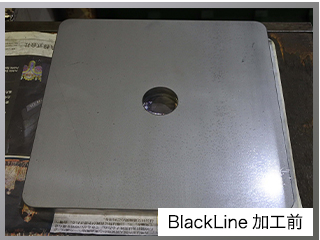
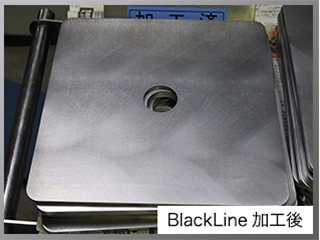
インタビュアー丸十様では最近、機械だけでなくオーセンテックのaCloudというソフトも導入されていますが、導入を決めた理由を教えてください。
松尾様:昨今のAIやIoTへの潮流は、板金業界も同様と考えています。仕事の効率化や工場の生産性をもっと上げていくためにも、デジタル化を進めなければいけません。最近のレーザーマシンやコンビネーションマシンは、ほぼネットワーク化されており、稼働時間等も把握できます。単体機といいますか、旧式のプレス機やボール盤などは稼働状況が分からないのが現状です。
そういった機械には安価なセンサーなどをつけて自前のIoT化で稼働状況や停止やサイクルタイムなどの状況を見える化しています。
その状況の中で、オーセンテックさんのバリ取り機や洗浄機は稼働状況やエラーの表示と清掃・消耗品の交換目安が分かる様になっています。オーセンテックさんがエラー監視をしてくれているのも助かります。データに関してもクラウド管理をしたいと思っている我々の思いと今回のaCloudはマッチしています。
“どの様にして付加価値を上げいくのか?”“どの様に見える化することで生産性を上げるツールとして生かせるのか”がとても必要なのだと思います。経営者と現場の共通の資料としてIoTデータや見える化というものがどちらにとっても、大事な検討材料になります。丸十では、すべての機械をIoT化していきたいのです。
インタビュアー丸十様では、機械設備以上に、今後は工場全体の管理としてシステムやソフトの導入が大きなアドバンテージになると考えているのですか?
同業他社が多い中で弊社も差別化をしていかなければなりません。そこでは、品質、コスト、デリバリーの全てに応える事が鍵となります。働き方改革もありますから、短納期だからといって現場にオーバーワークをさせるわけにもいかないし、もちろん納期を延ばす事もできない。いかにお客様のニーズに合わせるか、その為には最新の設備、ネットワークを導入して、そのニーズに応えていかないと次の世紀には残っていけないと思います。
今までも他社に先駆けて設備を取り入れてきたように、常に最新の設備を取り入れる事が弊社の強みになっていると思います。
インタビュアー最近では、企業に対して様々な制限や制約があります。時間の管理を含めた従業員を守っていく事も大事だとお考えですか?
松尾様:受注量が多い、仕事が忙しい、だから長時間残業がOKという時代ではないのです。社員の健康管理も考えた上で、求人も難しい中で、今、丸十では離職をゼロにして今いる人たちに安心して働いてもらいたい、健康でいて欲しいと考えています。弊社は、定年も65歳にしていますし、現在の従業員が19~72歳の幅広い年代の方が働いている中で、高齢者も若者も安心して働ける環境にしていきたいです。
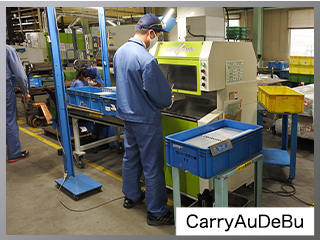
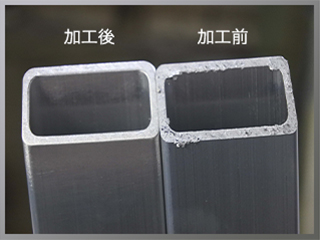
インタビュアー19年後に創業100周年を迎える丸十様のこれからの企業としての方向性をお聞かせください。
松尾様:モノづくりの社会は、今後も残っていくとは思います。ただ、そのやり方はこれからもっと難しくなってくると思います。少子高齢化の中で我々はどのようにモノづくりをするのか、弊社の弱い部分でもある設計開発は、M&Aで設計の会社と協力して開発したり、ベトナム工場だけではなく他にも東南アジアのこれから発展する地域で、更なるグローバル化を図りたいと思っています。
IT,ITC,そして5Gといった、これからの新しい情報を集めながら、未来のモノづくりを我々は考えていきたいですし、自動化や協働ロボットも視野に入れて、短時で今まで以上に生産性が上がる仕組みを考えていきたいと思います。そして、それは経営者と実際に現場で使う作業者が共に学ぶことであり共に考えていくことが最も大事で、そうすることで未来の成功へと繋がっていくのだと思います。
バリ取り機の導入ならオーセンテックまでぜひ一度ご相談ください。
その他導入事例