【導入機器】
AUDEBU 1000/洗浄機 AUDEBU Racoon
【事業内容】
精密板金加工の設計から製造、
IoT化を実現した物理セキュリティ
【選んだ理由】
AUDEBU Racoonを共同開発したことから
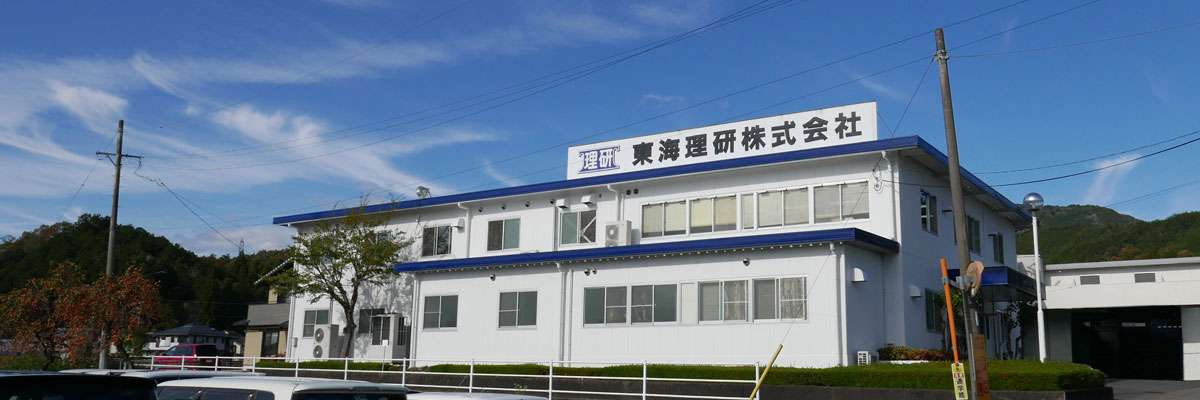
東海理研株式会社様の概要
東海理研の資源は「人」である=スイミー経営
絵本『スイミー』(レオ・レオニ作、谷川俊太郎訳)の主人公スイミーは、一匹だけ仲間と色が違う小さな魚。仲間とともにみんなを脅かす巨大な魚に立ち向かい、ついに勝利をおさめます。
ここに必要なのは、一匹一匹が個性・能力を認めあうこと。これを繋ぎ合わせるのが団結力であり、信念、志です。東海理研の社員たちは、常に思いやりの心を持って考えます。
「今、世の中に必要なものは何か」「私たちに何ができるか」「実現するにはどうしたらいいか」。
感性を研ぎ澄ませば、答えは自ずと返ってきます。当社の技術が板金からセキュリティ商品へと発展したのも、その一環です。
東海理研株式会社様 会社案内より
東海理研株式会社
岐阜県関市武芸川町谷口
http://www.tokairiken.co.jp/
インタビュアーAuDeBu Racoon(洗浄機)を導入するきっかけは何だったのでしょうか?
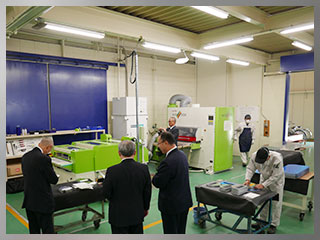
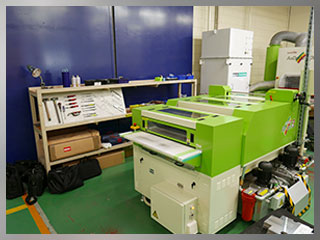
東海理研製造課長:弊社では、単品加工だけではなく、組立品(アッセンブリ製品)と自社開発製品の比重が増えてきた事から、各種部品を洗浄して組み立てる必要が出てきました。
(これまでの慣例から単品加工の場合、洗浄は組み立てを担当するそれぞれの会社さんで行っていましたので、弊社で洗浄機を導入する予定はありませんでした。)
このことから、生産ライン全体の効率化をはかるためには、導入済みのバリ取り機とは別に、時間のかかる洗浄加工を自動化し、時短するための洗浄機の導入は必須条件となっていきました。
バリ取り機は、オーセンテックさんのAuDeBu1000を導入していましたので、残る洗浄機の候補をいろいろと検討するため、数社に連絡をしました。
オーセンテックの髙田社長にもお電話で相談させていただきました。
その時、偶然にも現在、洗浄機を開発中であることを知り、髙田社長より「ホームページの動画を見て!」と言われ、さっそく洗浄機のデモを動画で拝見しました。
当時、仕事が込み合っていたこともあり、すぐに初号機をモニターとして貸し出していただきたいと申し出ました。
すぐに髙田社長より貸し出しの了承をいただけましたので、その後1か月間、弊社工場にて実加工でのランニングテストを実施させていただきました。
インタビュアーそんな中、最終的にAuDeBu Racoon(洗浄機)が採用された経緯は?
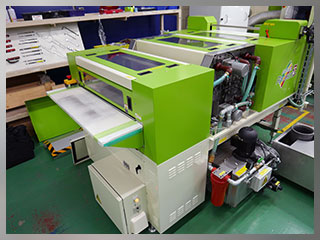
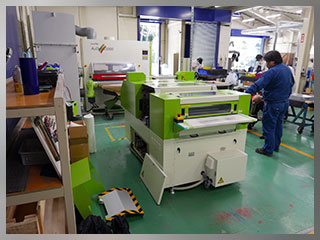
東海理研製造課長:導入するきっかけは、弊社社長と「どの機械を選定するか」の最終的なの打ち合わせの時の事です。申し上げにくいのですが、私はオーセンテックさんの洗浄機を選定しておりませんでした。
社長から「なぜオーセンテックさんを選ばなかったのだね?」と聞かれ、私は「初号機の現段階では、製品の洗浄、乾燥状態など、機械の完成度から判断するにまだ早いのではないかと感じています。 」 と率直な意見を伝えました。
一方、「オーデブ(導入済みのバリ取り機)の実績から見て、今後、さらに良い機械をつくられるのではないかと感じています。」とも伝えました。
すると、社長より「だったら、2号機を一緒につくればいいじゃないか!」というアドバイスをいただいたのです。
私の中で、最終候補を選定する際の基準は、機械自体の納入実績や社歴を重視する方針でいましたので、話の展開に驚きました。
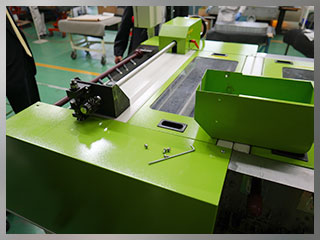
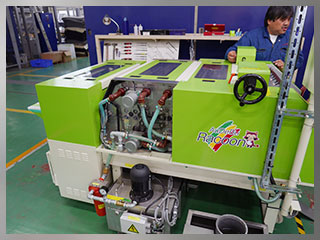
あの時の社長のアドバイスが私の背中を押し「オーセンテックさんと一緒に2号機をつくる」と言う大きな目標設定につながったのだと思います。
さっそく、この事をオーセンテックさんに相談したところ、快く引き受けていただけました。
私自身もさっそく、現場からの意見を集約し、27項目にも及ぶ、改善点リストをまとめ、オーセンテックさんに手渡しました。
それから1年ほどかけてつくりだされたのが、今回導入したAuDeBu Racoon(オーデブ ラクーン)なのです。現場の問題を真摯に受け取っていただいた結果です。
一口に1年と言いましても、現場からのフィードバックを元に一緒につくり出して行くのは大変でした。27項目の改善リストには、それぞれ「現象」「原因」「対策」「解答」に対する取り組みがあり、文字にしてしまえば、わずか数行の内容であっても現場と実際の機械の調整は、想像以上に大変なものがありました。
原因を明確にお伝えするにも、実際の工程の中から例えば「拭き取りだけで、月に70.5時間(約9日)も費やしていた」工程を洗浄機による自動化でどこまで効率を上げ、作業員の負荷を軽減し、かつ職場環境もより良いものに変えて行くのかを、目に見える工程表や作業時間管理表といった客観的な数字に落とし込んで行くのに骨が折れました。
また、途中の工程のワークがどのような状態になっているのかを目視するために、どうしても「透明な窓」が必要とのことから、機械製造のコスト高に通じる無茶な要望にもしっかりとお付き合いしていただけました。
その甲斐もあり「200枚の棚板を2名で半日(のべ8時間)かけていたものが、2人で1時間になった(のべ2時間)(1/4に短縮できた)」計測などから、あの時は、けっこう厳しい要望をぶつけるのも気がひける思いでしたが、今こうして実際の現場で使える機械として一緒に開発に参加できたことは現場にとっては本当にありがたい事です。
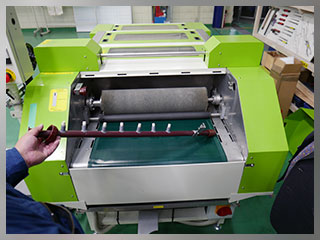
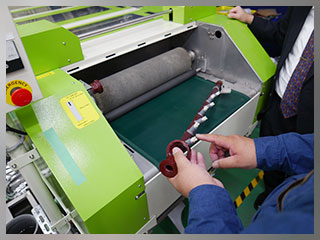
インタビュアー実際にAuDeBu Racoon(洗浄機)を現場でご利用になっていいかがですか?
東海理研製造課長:初期段階の機械では、最後の工程でワークに水がちょっとはねてしまい、結局手で拭く必要がありました。この事実を数字に置き換えると、水を拭くのに、3秒から5秒かかってしまい、ある案件では、水拭きだけで1週間近くもの時間が無駄になってしまいました。
水が残るとアルミの場合は腐食してしまうなどの問題もあり、拭き取り作業も自動化させる必要がありました。
その後の改良型の機械では拭き取り作業も完全に自動化するまでに進化させる事が出来ました。
全体工程の視点からは、バリ取り機のすぐ隣に洗浄機を配置することで、バリ取り加工と同時に洗浄し、全体の作業工程がリズム良く快適に流れるしくみを実際の流れの中で調整して行くことで、理想のラインにする事が出来ました。
前項でもお話ししたように、改良型のラクーンでは、「200枚の棚板を2名で半日(のべ8時間)かけていたものが、2人で1時間になった(のべ2時間)(1/4に短縮できた)」計測値や、他の案件においても概ね1/4から1/5程度の時間短縮を実現することが出来ました。
また、数字には表れない事になりますが、一番助かっているのが、作業員の健康も含めた職場環境の改善なのです。
これまでは、部品を洗浄する際は、ひとつひとつ手作業で拭き取り作業をしてました。中には、炭化水素系溶剤を使い拭き取る事もあります。炭化水素系溶剤は、洗浄力が高いですし、乾燥性にも優れ、拭きムラやシミが残りにくいと言ったメリットもありますが、一方で、可燃性への配慮や有機溶剤中毒予防対策(少量・短時間使用、風通し確保、マスク着用、等)を義務づけするなどのしばりもありました。
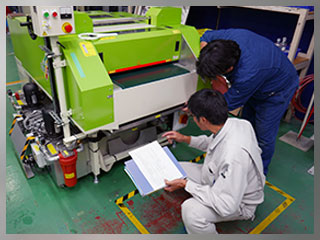
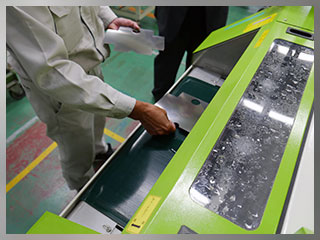
微量な使用であれば問題ないとは頭では思っていても、数日間に及ぶ手作業の場合は、炭化水素系溶剤の使用を出来る限り少なくしたりするなど、効率化とは、ほど遠い現実がありました。しかも単調な作業として数日間も同じ部品を拭き取る工程は、実際に作業を担当するスタッフに作業を依頼するのも気が引けますので、出来るものなら避けて通りたい工程でした。
さらに、タッピング複合機が主流となった今、タップの中に入った油をひとつひとつエアーで吹いていたものが、ラクーンのコンベアに流すだけでよくなったのは本当に助かっています。まれにですが、綿棒を使ってタップ穴の中の油をひとつひとつ拭き取る工程からも解放されます。
実は、タップの油やパンチの油は、一晩置くだけで製品がダメになってしまうんです。スムーズに一気に工程を流す事が不良品を出さないキモになっています。
インタビュアー職場環境の改善について、もう少しお話しを伺えますか?
東海理研製造課長:職場環境が本当に良くなりました。
これには、大きく三つの意味があります。
一つ目は、温水とジェット水流による洗浄を行う事で、炭化水素系溶剤をほとんど使わずに済む事。
二つ目に、仕事とは言え、同僚に頼みにくい作業をたのまなくて良くなった事。
そして、三つ目に、洗浄機から出てきたワークをそのまま、きれいな軍手で曲げ加工にまわすことができる事です。
これら三つの相乗効果により、アッセンブリ全体の工程を通じて、品質(油除去や拭き取りのばらつき防止)、効率性(ボトルネック工程の排除)、環境(直接的にも間接的にも気持ち良く仕事が出来る)、をそれぞれ保持したままの状態で、曲げ加工に進めるメリットはとても大きいですね。
整理整頓されたクリーンな環境で仕事に取り組んでほしい、地元の美しい環境にご迷惑をかけない配慮など、根本的な考え方として、クリーンレベルに対する思想が弊社とマッチしていた点が一番大きいと思います。
半年おきに実施している粉塵テストにおいても、バリ取り機と洗浄機を設置している部屋も他の部屋もクリーンレベルは、ほぼ同じレベルとなっております。
インタビュアー今後の展望についてお聞かせください。
東海理研製造課長:今後、益々アッセンブリ製品や自社開発製品の比率が高くなると予測しています。部品単体の品質はもちろんの事、二次加工としての溶接、組み立て、塗装、さらには梱包まで含めたトータルな完成品の一貫生産を任せてもらうことで、お客様のご負担を軽減するサービスを今まで以上に展開させて行きます。
アッセンブリ形式へのお客様のご要望は「この会社にまかせれば、常に同じ品質で戻ってくる」ことを期待しているのだと思います。A社、B社、C社、から別々に集めてきた部品をD社で組み立てるよりも、A社で部品作りから組立まで一貫して行うことで時間短縮は勿論の事、組立の工程差や人的・機械的な品質の差異を生みにくいシステム、さらに移動時間や管理体制の一元化など広範囲における生産ラインを常に一定品質を保てることが一番のメリットではないかと考えております。
近年では、指紋認証、顔認識、ログ管理、と言ったITとも融合したセキュリティ関連製品の比率も増えてきましたので、より一層の総合力を問われる案件を取り扱う体制が不可欠となっています。今、話題のマイナンバー関連の製品も開発する予定です。
一貫生産による生産ラインの要は、無理なく歪みなく計画性を持って各工程を組むことです。このためには、Aさんが拭き取り作業をすると30秒かかるが、Bさんが作業すると1分かかると言った作業時間差の平準化をはかる事や、拭く時の圧迫具合、拭きムラ、拭き残し、などのバラツキを抑え、品質を均一化する事が全体の流れをスムーズにするコツだと考えています。
この際、バリ取り機にしても洗浄機にしても、ベルトコンベヤーのスピードと流すワークの数と密度で基本的な生産量と納期の割り出しは出来ますので、計画性のある段取りを組む際にとても助かっています。
最終的に全体の工程を組み立てる際は、何と言っても人のリズムやテンポがとても大切な要素となりますので、機械に任せる所は機械に任せ、人に任せる所は人に任せ、お互いの能力が最大限発揮出来るしくみづくりが今後の私たちの発展を左右する大きなテーマでもあります。
AuDeBu Racoon(オーデブ ラクーン)の導入に際し、お互いに培った技術と熱意によるものづくりを、またご一緒に出来る事を心から期待しておりますので、今後ともどうぞよろしくお願いいたします。
バリ取り洗浄機の導入ならオーセンテックまでぜひ一度ご相談ください。
今回ご紹介した商品
その他導入事例