【導入機器】
ブランク材簡易洗浄機 Racoon800
【事業内容】
医療機器、情報機器や半導体など、
様々な分野の板金加工
【選んだ理由】
安定した仕上げと品質を保てる
「継続性」に魅力を感じた
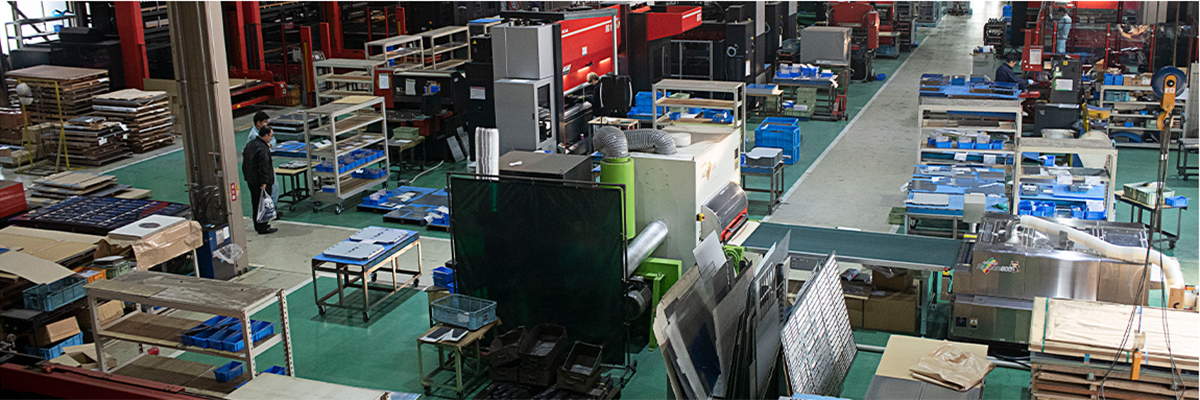
三条精密工業株式会社様
の概要
三条精密工業株式会社は1952年(昭和27年)に設立され、設立以来時代の流れと共に、プレス加工から精密板金加工へと大きく躍進を遂げてきました。
お客様の利便性を常に第一に考える「精密板金加工分野のコンビニエンスストア」としてお客様の幅広い注文内容と加工内容に応える事ができるよう日夜技術を進歩させてきました。
長年にわたり培った技術力と設備力、そして挑戦する気持ちを忘れずに「メーカーのために有益で高付加価値な製造業」であることを日々追求しています。
三条精密工業株式会社
新潟県三条市大字金子新田乙49714
http://www.sanjyo-seimitsu.co.jp/
インタビュアー今回は、三条精密工業株式会社 専務取締役 丸山様にお話を伺います、まずは事業内容を含めた御社の紹介をお願いします。
丸山様:三条精密工業は従業員が34名の会社です。創業から数えると今年で70周年を迎えます。
プレス加工業として創業し、約30年前から板金加工の比率が増え現在では全体の80%となっています。
メインとなる板金部品の仕向先業種・分野は非常に広く、医療機器の部品関連加工品の比率は全体の3割弱を占めています。情報機器や半導体、各種産業機械などの需要も高く、製造装置の部品や建材なども一部扱っています。
インタビュアー非常に多くの分野に関わりを持っているのですね。やはり時代や時流によってお客様業種の割合は大きく変わってくるものですか?
丸山様:そうですね。例えば7年程前に携帯電話の法人回線が出回った時には、基地局向け4G業界向けの受注が膨らんだ事もありましたが、世の中の流れでさほど仕事量が左右されているとは感じません。医療機器は安定して一定の基準を持っていますし、今後も安定的な受注を見込めると思います。
弊社は多種多様な製品を扱っていますが、メインクライアントになるところでも売上比率は全体の2割強です。
一つの業種やお客様に依存しない様に約15年位前から様々な分野で仕事を頂くよう心掛けており、何かあった際にはリスク分散できる営業をしています。
インタビュアー幅広い業種のお客様を持っている中でお客様の共通する要望や傾向・パターンなどはありますか?
丸山様:最近では、小ロットを希望されるお客様が多くなっています。弊社もそこに着目し、適した設備への更新を行なっています。
例えばプレス加工品の場合は1000個~3000個の注文数になるので、平均すると1ロット100個前後くらいですが、板金加工品を含めた弊社の受注品全体では、だいたい1ロット5個~6個が平均値です。100個~200個ができる業者は他にもたくさんありますが、小ロットに対応できる業者は少なく、弊社はたとえロット数が1個でも仕事を受けます。そこが多くのお客様から重宝されているところだと思います。
インタビュアーホームページを拝見して、御社は非常にユーザー寄りの会社であると感じております。そんな三条精密工業様が今回オーセンテックの設備を導入したきっかけにはどのような背景があったのですか?
丸山様:3年位前にお客様から、加工品を納品した際「埃っぽかったり油っぽいことがあったので、ふき取り作業をしっかりやってほしい」と言われた時期がありました。色々な洗浄機を調べてみましたが、なかなか良い洗浄機がありませんでした。弊社は多品種小ロットの仕事が多く、日々概ね3000アイテムの製品が流れており、しかも製品の大きさもまちまちなので洗浄機の選択は非常に難しかったのです。
その後受注数の増加に伴い洗浄後に人力でおこなう手拭き作業ではとうてい納期に間に合わない状況となり、現状の従業員で納期内に収めるには各工程間の段取りの速さをどれだけ縮められるかが鍵でした。洗浄機以外の設備はある程度ネットワーク化されていて工程の時間も読めるのですが、洗浄後の加工品を一枚一枚手拭きで行うと一枚あたり30秒以上掛かってしまい全体の仕上がる速度が落ちてしまうというジレンマに陥ってしまったのです。
洗浄工程が必要なお客様には「拭く」工程も含んだ見積り金額をご提示していますが、見積段階で「脱脂」「油汚れ」「汚れ」に関する指示がない状態での納品の場合でも、お客様は綺麗な状態での納品を望んでいます。コストを見込んでいないところに更に人件費をかけるのは経営としても非常に厳しいので自動化したいと改めて思ったのです。
社会的にみても少子高齢化が進んでいますし、弊社の従業員もこれから5~6年経過すれば、4分の1は定年を迎えてしまいます。少子化の影響で若い人が集まらない。でも仕事量は今と変わらない。今と変わらない仕事量を安定的にしかも品質を保った状態にする為にはムダを省いていかないと作業者の負担が増える一方です。その中で加工品の洗浄という作業は非常に大きな負荷となっていました。
Racoon800導入前の洗浄工程では、バリ取り後に、洗浄を行って、それらを一枚づつウエスで手拭きをしていました。この作業には、加工する時間と同じくらい時間が掛かっておりこの無駄な時間が無くすことができれば作業者の負担を大幅に減らせると思っていたのです。
インタビュアー多くの洗浄機メーカーや装置の中で、AuDeBu Racoon(オーデブラクーン)を選んだ理由を教えてください。
丸山様:一番の決め手は、「サステナブル(継続性)」ですね。オーセンテックさんのAuDeBu Racoonが安定した仕上品質を保てる事(=継続性)に魅力を感じて導入を決めたのです。他社の装置は一定時間を使うと洗浄力が落ちる懸念がありました。
実際、比較した各社ワークの洗浄サンプルを見た時には出来栄えはどこのメーカーもあまり差はなかったのですが、継続的に品質を落とさず、一日そして一週間と同じ品質で稼働できるかといった点では、このマシンに比べて他社では難しいと判断したのです。
現在は、導入後2か月半ほどたっていますが、品質に対する問題は起きていません。全体の工程として捉えると約2割位リードタイムが縮まりましたし性能に関しても大満足しています。
インタビュアー導入の決め手として、Racoon 800(ラクーン800)の継続性を評価されましたが、他にも決め手となる特長がありましたか?
丸山様:Racoon 800は、洗浄時に水道水をそのまま使用している点ですね。水道水の水質は常に一定であり劣化することはありません。しかも足りない分は簡単に補充もできます
またワークの材質を選はず洗浄できる点も魅力ですね。定期的なメンテナンスのみで一定の効果を発揮してくれるのは非常に評価できる点ですね。
また、ワークの表裏両面が1回通しで洗えるという点も大きな利点です。弊社ではバリ取り機(AuDeBu 1000)でバリ取りをした後にワークを洗浄しています。オーセンテックさんのAuDeBu Racoonは、両面を同時に洗えるので作業工程や作業時間の面でも非常に助かります。
パンチング/タップ油だけではなく指紋やワーク搬出に使用するアンローダーの吸盤跡もきれいに洗浄する事が出来ます。
またマシン導入時には当たり前だと思っていた事なのですが改めて考えると加工品が乾燥して仕上がってくれるのは品質の面でとても大きなメリットが有りますね。
インタビュアー「乾燥が甘いと残った水分が水染み(ウォータースポット)になってしまう」といった話を聞いたことが有りますがAuDeBu Racoonではいかがですか?
丸山様:搬出後のワークに水滴が残っていたことや水染みが発生した事はありません。バーリングやタップ、成形のある製品でも製品の出来栄えは安定しています。製品の乾燥状態を都度確認する必要が無いので、製品はスムーズに後工程へ流れています。洗浄後の製品が完全に乾燥しているので使っていてストレスが無いです。
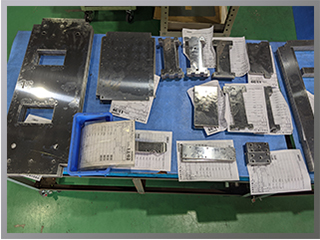
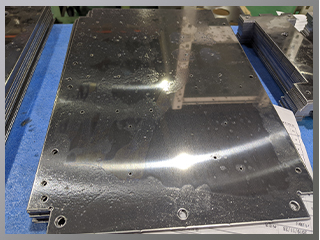
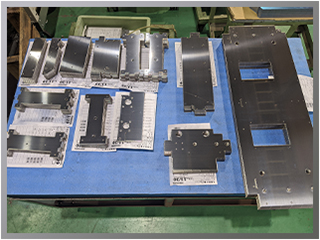
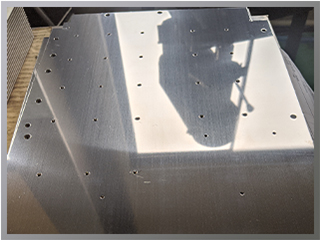
インタビュアーAuDeBu Racoon(オーデブラクーン)の導入後に、加工品の仕上がりとして気になる点などはありましたか?
丸山様:今までの手拭き作業だとタップの中の汚れまでは取れないし、拭いているうちにウエスに汚れがしみ込んでしまい、そのうちいくら拭いても汚れを塗り広げるだけになってしまいます。
AuDeBu Racoonを導入してからは、タップの溝に残る油や、パンチ/レーザー複合機のブラシテーブルから転写した油+粉塵汚れも非常に良く取れ、安定した仕上がりの製品を後工程に供給できるようになりました。
工場内でも部品1個1個の指示書の中で「ラクーン洗浄後取扱注意」といった記載をし、後工程で汚れが付かないように気を配っています。
インタビュアー三条精密工業様ではAuDeBu Racoonをバリ取り機(AuDeBu1000)とコンベアで繋げて使用されていますがどういったメリットがありましたか?
丸山様:弊社では多品種小ロットの加工品を扱っているので
- バリ取り機を通して洗浄もおこなうワーク
- バリ取り機は通すが洗浄はしないワーク
- バリ取りはしないが洗浄はするワーク
など製品の特性によって仕上げの方法を変えなくてはなりません。
会社としては、洗浄の工程にかかる人件費を減らす為に、バリ取りと洗浄を一気通貫で行なうという工程を望んでいました。
この場合、ある製品群には非常に高い生産性を発揮できますがそれ以外の製品でバリ取り機と洗浄機が別々に使いたい時に困ってしまう。この問題をクリアするためにはバリ取り機と洗浄機の間にバッファーが必要でした。
そこで、二つの装置にバッファーを持たせるためにコンベアを用意しバリ取り機と洗浄機の両方に製品を通したいときはコンベアを回して両方の作業を行い、バリ取りだけの場合はコンベアを止めてコンベアの上で品物をピックアップする。そして洗浄機のみを使用する場合はコンベアの上で洗浄作業のセットを行うという様に、どのパターンの製品でも対応できるようになり、当初の人件費を減らしながら仕事の幅も広げる事ができたのです。
インタビュアーオーセンテックに今後、期待することはありますか?
丸山様:板金加工の工程において手作業が必要なところがあります。そういう作業を簡易化できる装置があると嬉しいです。オーセンテックさんの設備ラインナップでは、バリ取りの工程は自動でバリ取り機を通せば綺麗に落とせるのですが、パンチプレスは必ず製品の角にジョイントが残ってしまうのでバリ取りは自動化できてもジョイントの除去は自動化できていません。そのため、今は専属の作業員がひたすらジョイントを落とし続ける作業を行なっています。加工品の品質を保つためには、必ずしなければならないのですがこの作業を能力がある従業員にやらせなければならないのはもったいないと思っています。ワークをセットしたらジョイントを一度に全部落とせるような装置を是非開発して欲しいですね。
また装置のコンディションを管理するIoTを使った仕組みがあれば嬉しいですね。例えば、“ここが劣化しています”というのを機械が感知しオーセンテックのサービスセンターの方から連絡がくる、というように先回りで教えてもらえると今後の工程管理や工場経営に大いに役立つと思います。
インタビュアー最後に三条精密工業様の今後の展望についてお聞かせください。
丸山様:人が間違いなく足りなくなってきます。最低限の人数で最大の効率を上げられる設備投資が必要だと思います。
しかし、設備があるだけでただ機械に頼っただけではどこでもできる加工になってしまうので、従業員には機械の特性を熟知した上で加工を進めていけるようスキルアップを期待しています。
それができれば品質も納期も全うする事ができると思いますので、社内のスキルレベルを上げ、そして自動化できるところは自動化を進めていくということが弊社の今後に必要かと思います。
バリ取り洗浄機の導入ならオーセンテックまでぜひ一度ご相談ください。
その他導入事例