About Deburring
"Deburring Mechanism" Based On Consideration Of Engineers
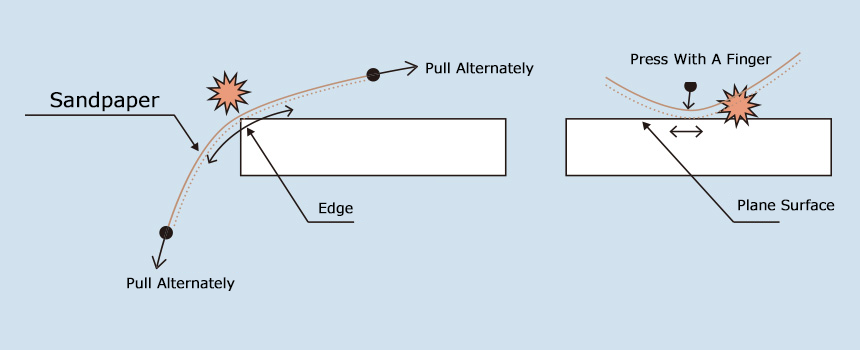
Not more than deburring machine.
1. Firstly
Recent years, deburring machines mounting polishing brushes, including AuDeBu, have become popular in sheet metal factories. This type of deburring machine removes the burrs by rubbing or striking by the sandpaper which is used on the polishing brushes as material, on the surface of workpieces. However, in the field, products come in various shapes. Besides, the actual situation is that the placement of the workpieces inside the deburring machine is also various situations.
The relationship between burr and brush, that is, the direction of rubbing and the edge with burrs, is often not placed parallel. This should be greatly influenced and of course it will make finishing bad, but, actually, there is no problem with finishing. The reason is that even if the brush hits unevenly, it polishes well in some form, and it is thought that the deburring mechanism of the machine is likely to be different from the idea from manual work.
Before we get into the mechanics, we will compare deburring manualy by hand and by the machine..
Round chamfering can be done by rubbing the edge with sandpaper a few times as shown below.
Rubbing a plane surface will cause deep scratches immediately.。
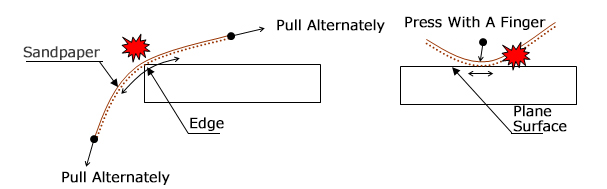
The edge can not be chamfered by several rubbing of the deburring machine which the polishing brush rotates. Also, there are no deep scratches can be seen. The difference is that one side of the sandpaper is free, that is why almost no friction.
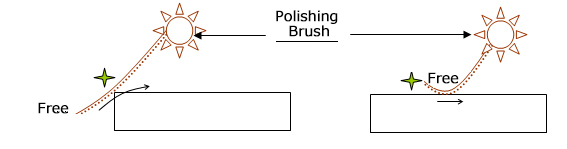
If it is thought that sandpaper rubs and removes burrs, in order to remove the burrs that exist in all directions of the workpiece, a fixed idea that “the polishing surface must be averaged in every direction” will appeared. However, the machine that removes the burr by rotating the sandpaper brush like AuDeBu seems to be different concept from the manual work.
2. Working depth and track of polishing
The polishing brush which rotates and chamfers the edge, the brush depth is set deeper than the surface of the workpiece. The polishing time for one brush is as shortly as 6.3 ms. When the working depth is 8 mm (as standard), the path from the start of polishing to the end of polishing a single brush piece is as shown below. If calculated the radius of the polishing brush as 150 mm, the polishing length passing on the workpiece is 96.7 mm. We will investigate the mechanism of deburring using this one track of polishing as a rubbing model. If the rotation speed of the spindle is 1000 rpm, one rotation is 60 ms.

3. Why the edges and burrs are intensively polished
When looking at this rubbing model in time sequences until polishing brush rubs on the product and passes through, the brush first collides with the workpiece and polishes. The energy at the time collision is "proportional to the weight of one brush piece ×(multiplication) the square of the spindle rotational speed". The collision time is very short, better to say that ”brush strikes the workpiece” . After hitting, the brush is rubbed and polished, but the force pressing the brush is the centrifugal force comes from the spindle rotation. When striking or rubbing, the brush piece is light and soft, so that the polishing force on the sanding part of the rubbing model will be very small. The image below shows the state of the force during polishing.

Also, when the energy of the collision site collides with the plane surface, it is distributed in the size of the site (8 × 4 = 32 mm 2). On the other hand, if the collision position is at the end of the workpiece, the polishing force is calculated to be 40 times that of the plane part, assuming that the width of the edge of the end (0.2 mm) × the width of the brush 0.8 mm . In addition, the more the burr is sharped whete the collision is concentrated, the more concentrated the power on the burr. "The polishing is concentrated on the burrs and edges, but the surface of workpiece is not polished." This is what the characteristic of the deburring machine is. We think that "the burrs are not rubbed but stiked." When the chamfering by the strike force, the brush piece is soft enough that the direction of the edge direction is does not matter if it different, and the collision site bends flexibly as shown in the figure. Therefore it is not necessary to rub at right angles to the direction of the edge.

4. Invisible "Twist" and "Sway"
Why is no difference appear in the finish? Next, rotate the rubbing model and observe in detail. The speed component due to the own brush shaft rotation shown in the figure is a force generated by the friction with the product and never occur unless the product and the brush come into contact. Due to this velocity component, a force acts in the outward direction in the front away from the turning direction and in the inward direction at the rear, and an invisible “Twist” occurs around the spindle axis.

This “Twist” does not occur if the working depth of the brush is zero from surface, but if the working depth is deeper than surface, it will occur on any machine by brush turning.
If chamfering of 0.2R is achieved by 10 seconds of polishing with actual deburring, the number of times this rubbing model polishes will be 10000 (ms) / 6.3 (ms) = 1587 times.
The edge position of the workpiece moves, but the rubbing model is repeated continuously one after another and polish this edge position.
It is calculated to be 0.00013R by one brush piece polishing
Next, the figure below shows how the polished brush piece makes one rotation and polishes for the second time. During the 60 ms of one rotation of the brush, the advancing angle is 5.77 degrees. The rubbing model of the brush piece on the outside and inside of the cylinder polishing brush at that time is as follows. From this figure, it can be seen that a circle is drawn with the width of the brush piece just below the spindle axis, but about 4 mm of rolling occurs at the start or end position of the rubbing model. ( location at ◎) Continuous "Twist of the brush" leads to "Sway" . This rolling phenomenon works over the entire circumference and works effectively in all directions. This hidden function that is not inferior to the deburring finish is called "Small rolling" in our company. The movements of each brush while swaying are look like "Hula dancing".

5.Afterword
Many engineers have explained the mechanism of deburring as a rubbing model, which is the key point when considering the introduction of deburring machines. I hope that it will stand as a guide when considering the deburring mechanism. However, the mechanism of deburring is deep. Not more than deburring machine.